For most of its history, RBM (Richards Bay Minerals, a 5000-people mining and processing business in South Africa) had been challenged by tragic safety incidents. In its first thirty years, a member of the workforce lost their life every 14 months - a confronting industrial safety challenge by any yardstick.
In 2024, over ten years since Rio Tinto took control, it has been more than five years since there was a fatality at RBM. It is now among the most advanced heavy industry operations in South Africa and a world class business. How was this achieved?
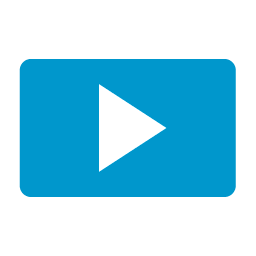
Rethinking safety
In 2010, Rio Tinto’s group executive team approved a new 5-year corporate safety strategy, developed with ERM. It aimed to break through the plateau in the group’s fatality rate. The strategy’s centerpiece was a new approach to supporting the leadership teams of sites to achieve step changes in safety performance: the Site Safety Acceleration Process (SSAP).
SSAP was different to other approaches in the industry at the time. It cut to the core of an organization’s social processes, revealed the attitudes and cultural norms that blocked or limited people’s ability to work effectively together, and created new pathways and coalitions for change. It involved a joint team of workforce change agents, working alongside the management team.
ERM’s critical part was to listen deeply, to find out how people really felt about their work and their colleagues, and to bring the toughest issues out into the open for confrontation and resolution. Senior leaders were able to see clearly where the problems lay, even when they, themselves, were a part of them.
Only when the roots of rivalries, resentments and ‘us v them’ attitudes were understood, could solutions be developed. It was the dynamics of change agents and managers sparred together through the process, the experience of joint discovery and a shared disdain for the status quo that was, in fact, transformational alchemy.
Within three years, the process was run at the group’s top ten largest and highest risk assets, most of which had experienced fatalities in the previous three years. These interventions revealed that whether in Australia, Canada, USA or Europe, everyone at every level wanted to do a good job. Yet each site had its unique challenges and needed unique solutions. These were rarely technical; Rio Tinto has world-leading work routines and safety tools – the mission was to bring them to life through a deep leadership and cultural re-set.
In the ten years that followed its launch, twenty-five Rio Tinto assets undertook SSAP, six of which went on to gain the coveted annual CEO’s Safety Award. In most cases, these assets were not only recognized for becoming safe operations, but for becoming great businesses. Perhaps the most remarkable of these is RBM.
Richards Bay Minerals, South Africa
Deconstructing the ‘old ways’
Rio Tinto took full control of RBM in 2012. Werner Duvenhage, a highly experienced operational leader, joined RBM in early 2019. He knew that prior to Rio Tinto’s acquisition, fatalities had been almost an annual occurrence. No stranger to industrial settings in the region, Werner saw that RBM had the ingredients to achieve a leap. He invited ERM to run a SSAP.
Werner signaled his intentions: he promoted a few high-potential mid-level leaders into senior roles. He then assigned a team of fifteen change agents, deliberately ensuring a racial and gender balance, to work with ERM in the SSAP effort. Their role in the discovery phase was to probe into ‘why’ things happened the way they did. Then in the co-design stage, they worked alongside senior managers - people they had never even spoken to before – and brought pragmatism to solution design.
The findings of the joint team’s discovery work were explained to Werner and his management team in the open forum of the site’s Indaba (a Zulu term for ‘important village discussion’). When the feedback was done there was an uncomfortable pause; then a senior union representative raised his voice and said, “these findings aren’t correct - they are ABSOLUTELY correct!”.
RBM’s safety transformation begins
During the following week Werner surprised his organization - and won people’s respect in equal measure - by personally leading various worker consultation events:
- He called a meeting with 100 supervisors. They explained their conflict in balancing safety commitments to their teams with other demands placed on them. The discussion, moderated by ERM, gave everyone a chance to state their case, debunk rumors, and figure a way forward. Not everyone was happy, but everyone felt heard and trust in the leadership team rose; and
- He organized another off-site meeting, this time with 200 women. For the first time, they felt their leader wanted to hear about the realities females faced daily, e.g., sexual harassment, bullying and belittlement. ERM moderated an outpouring of honest, eye-opening, and disturbing revelations. The leadership team listened with a simmering sense of outrage. Werner made clear his zero-tolerance for bullying and harassment and gave a firm commitment to make things better.
The managers, employees and contractors of RBM were not used to this level of direct contact and transparency. Werner was not appeasing – he was candid and principled. People saw how committed he was to improving working conditions and transforming operations. He stated what he expected from his leaders and from his people. His leadership team quickly began to mirror him. Hope began to take the place of frustration and resignation.
In the following months, the six improvement teams set out to drive their solutions into the fabric of the operation.
Co-designing practical solutions
Lasting effects of deep transformation
ERM caught up with Werner at the 2023 annual mining conference in Cape Town. He explained that prior to SSAP in 2019, RBM had been among the lowest rated assets on Rio Tinto’s group-wide safety maturity scoring. By 2021, they were among the ‘most improved’ and by 2022, they were among the best and had just been granted the 2022 CEO’s Safety Award!
All six SSAP workstreams contributed to the transformation which led to RBM winning this prestigious award.
Werner highlighted:
- ‘The Guests in our House’ workstream (contractor integration) had replaced service providers’ feeling of being ‘unappreciated outsiders’ to one of ‘part of our team’. RBM had become a best-in-class reference across the entire Rio Tinto group.
- ‘The Security of our People’ workstream had flipped the security team’s priorities from ‘protecting property’ to ‘safeguarding people’, which lifted a huge sense of anxiety for the nightshift teams; and,
- The ‘Women in the Workplace’ workstream had led to a sea change. First, physical conditions had been tackled. Then the prejudices, liberties and transgressions were appropriately dealt with, and new attitudes instilled. Werner conceded that this had proven even more complex than anticipated. Yet what his team had already achieved was groundbreaking in the industry.
In 2023, some ten years since Rio Tinto took control, it has been more than five years since there was a fatality at RBM. It is among the most advanced heavy industry operations in South Africa and a world class business. Bravo, team RBM!
Transforming lives for years to come
For further information:
Jonathan Molyneux
Senior Partner, Strategic Programs
jonathan.molyneux@erm.com
T: +44 (0)7912 086 667